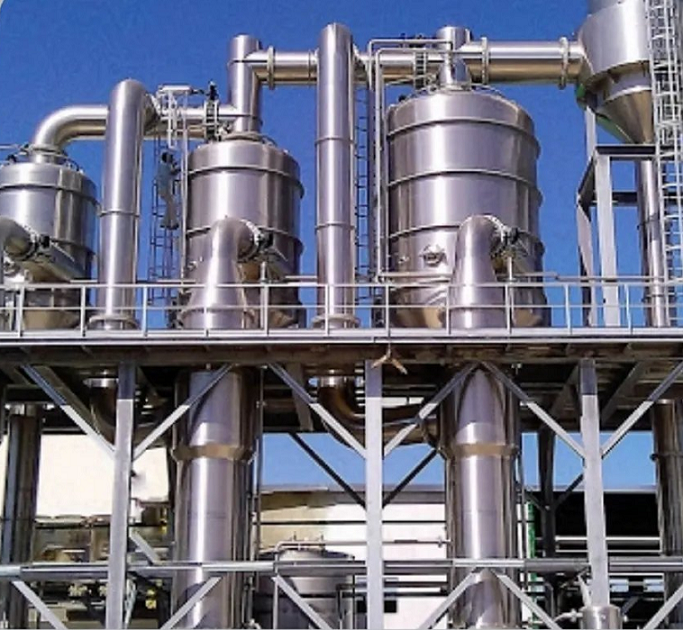
Introduction:
Water storage is a critical component in the operations of chemical plants, where stringent standards are upheld to maintain purity, durability, and safety. Among various materials used for storage, stainless steel has emerged as a preferred choice due to its exceptional properties. This article explores the significance of stainless steel in water storage for chemical plants, highlighting its advantages and applications.
Durability and Corrosion Resistance:
One of the primary reasons stainless steel is favored in water storage is its remarkable resistance to corrosion. Chemical plants handle various aggressive substances, making corrosion a major concern. Stainless steel, particularly grades such as 316L, contains chromium and molybdenum, which enhance its ability to withstand corrosive environments, preventing rust and material degradation. This ensures the longevity of storage tanks, reducing maintenance costs and the risk of contamination.
Preserving Water Purity:
Chemical plants require high-quality water for processes such as dilution, cooling, and chemical reactions. Contaminated water can lead to undesirable reactions, affecting product quality and safety. Stainless steel does not react with stored water or release harmful elements, ensuring water remains uncontaminated. Unlike some other materials, it does not leach chemicals into the water, preserving its purity and meeting stringent industrial standards.
Strength and Structural Integrity:
Stainless steel boasts high tensile strength and durability, allowing it to endure extreme pressure and temperature variations. Chemical plants often store large quantities of water, and storage tanks must withstand heavy loads without compromising structural integrity. Stainless steel tanks are designed to handle these demands, offering a long-lasting solution resistant to mechanical stress, thermal expansion, and environmental factors.
Ease of Maintenance and Longevity:
Compared to traditional materials like plastic or mild steel, stainless steel requires minimal maintenance. Its non-porous surface resists bacterial growth and biofilm formation, reducing the need for frequent cleaning. Additionally, stainless steel tanks have an extended lifespan, eliminating the need for frequent replacements. This long-term reliability leads to cost savings and operational efficiency in chemical plants.
Environmental Sustainability:
Sustainability is a growing concern in industrial operations. Stainless steel is an environmentally friendly choice as it is 100% recyclable, making it an ideal material for eco-conscious companies. Unlike materials that degrade and contribute to environmental pollution, stainless steel can be repurposed without losing its quality, reducing waste and promoting sustainability in the chemical industry.
Applications in Chemical Plants:
Stainless steel storage tanks are used in various applications within chemical plants, including:
Process Water Storage: Maintaining water for chemical processes while ensuring purity.
Cooling Water Storage: Used in heat exchange systems for cooling reactors and machinery.
Emergency Water Storage: Providing backup supply for unforeseen circumstances such as fire hazards or system failures.
Wastewater Treatment: Holding and processing water before disposal or reuse within the plant.
Conclusion:
Stainless steel has established itself as an indispensable material for water storage in chemical plants. Its corrosion resistance, strength, purity preservation, and sustainability make it the ideal choice for industries requiring reliable water storage solutions. Investing in stainless steel ensures efficiency, safety, and long-term benefits, helping chemical plants maintain optimal operations with minimal environmental impact.